Cutting Carbon Fiber with a Waterjet, Advantages and Disadvantages
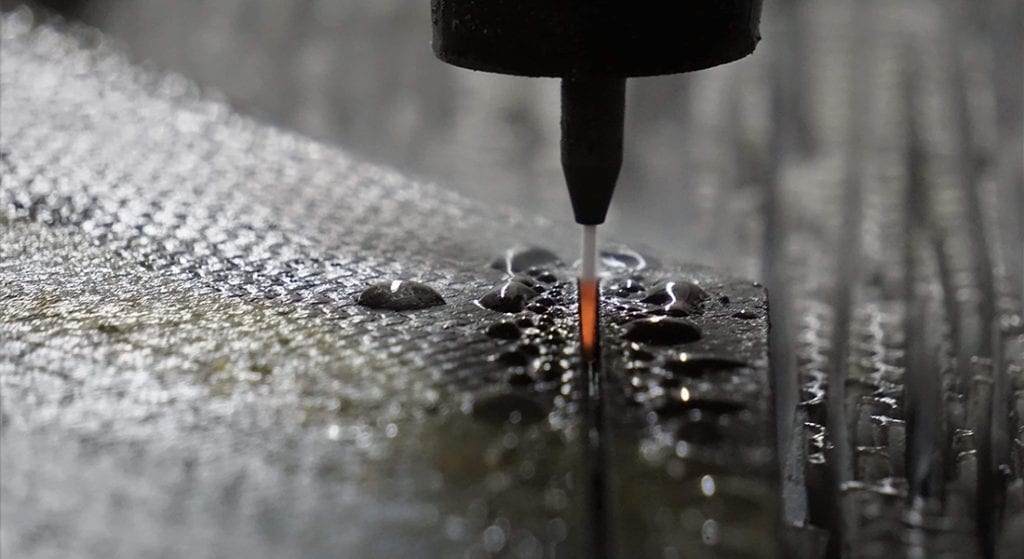
What is a Waterjet?
A waterjet uses a pump to create a high pressure (up to 90,000 psi) jet of water that can cut through anything from foam to 8+” steel plate. When cutting through metal or carbon fiber, an abrasive material, such as garnet, is used to aid in the cutting process. (See the "Source" links at the bottom of the post for more information on how Waterjets work.)
Now let’s look at why a waterjet is such a good tool for cutting carbon fiber.
Part thickness
One huge advantage of the waterjet is that it can cut very thick carbon panels with relative ease. With a router, thick parts require more passes which takes time and causes more wear on the bit. You also have to worry about clearing out chips and dust from deep slots. Additionally, with the proper tuning you can easily cut small features that would be impossible on a router due to the depth.
Speed
Cutting speed on a waterjet, especially for small features, is much faster than using a router. With a router, the depth of cut and feed-rate depends on the size of your router bit and part thickness. Smaller bits and thicker parts require multiple passes, whereas a waterjet can cut the same part in one pass and usually with a faster feed rate.
Dust Prevention
Another major advantage to using a waterjet is the dust containment. One of the main concerns when working with carbon fiber is dust. Carbon fiber dust can find its way into the inner workings of your machines and cause parts to grind or wear faster than they normally would. It is also an irritant if inhaled or can cause itchiness if it gets on your skin. With a waterjet, all the carbon dust gets blasted into the water tank where it is easier to handle for proper disposal. No expensive dust evacuation systems are required.
Tight cut patterns
The jet diameter of a waterjet can be tuned to roughly .025 inches, this will allow for designs with very small holes or internal features to be cut. This tool diameter can also be used to cut fairy close to an internal square geometry.
Disadvantages
While there are many advantages to using a waterjet for cutting carbon fiber, there are some drawbacks as well. The next few sections will address these areas.
Edge Finish
Because a waterjet uses an abrasive to cut through the strong carbon fibers, the edge can have a slightly rough surface. This can be controlled with the garnet mesh size (the finer the abrasive, the finer the finish) and with the feed rate. While for some parts this finish is acceptable, other parts will need to be sanded to get a smoother finish. The time spent cleaning up the edge may offset some of the advantage gained from cutting the parts on the waterjet. There is a balance between cutting speed and part complexity to consider if running a large volume of parts.
Blowback
Another area of concern when cutting carbon fiber is the blowback that comes from passing over one of the slats. The waterjet tank uses metal slats that span the width of the tank and provide a surface to support your work material. When the high-pressure jet passes over the steel slat, the jet of water and abrasive can be deflected up which essentially sand blasts the back side of a part. Typically, this wouldn't be noticeable on a metal part, but it could ruin a part of the surface of a carbon part.
Fortunately, there are solutions that exist to solve this problem. At Elevated Materials we cut our parts on top of a Rhino board. The Rhino board is made up of HDPE “straws” that allow the jet to pass through without blowing back toward the carbon. Its small cell size allows us to cut small and intricate parts without worry that they will fall into the tank.
For high volume projects of relatively large size, we create fixtures that protrude from the bottom of the tank that ensure the jet will only be cutting over water. Parts are then held in place using suction cups. With these fixtures we have cut over 1000 of the same part and haven’t had to change out any major components.
Delamination
Another challenge of cutting carbon fiber with a waterjet is piercing holes. The high-pressure water jet can eat away the resin between the carbon fiber layers and cause separation or delamination, which weakens the part.
Many manufactures will pre-drill holes on another machine and then bring the part on to the waterjet for cutting. The disadvantage to this method of course is the risk of mis-aligning your waterjet cut path with the holes that you pre-drill.
At Elevated Materials we have invested much of our time and resources in perfecting our method of piercing carbon fiber to prevent delamination. The technique has everything to do with lowering the pressure of the jet to around 10KSI (10,000 psi) and ensuring that garnet comes out of the nozzle prior to the high-pressure water. We use a vacuum assist valve that pulls the garnet through the nozzle before the jet turns on ensuring that the garnet hits the part before any water. If high pressure water hits the part by itself, your part will delaminate.
We’ve pierced and cut parts over an inch thick without any delamination.
Tapered Edges
Another concern that must be worked through with waterjet cutting is tapered edges. Since a waterjet is a high-pressure stream passing through a nozzle, it expands the further it travels from the nozzle. Depending on how far away your part is from the tip of the nozzle determines how expanded your jet is when it reaches the part you’re cutting. The farther the part is away, the more your jet can expand. An expanded jet leaves a sandblasted look and a lower quality, slower speed cut.
Edge taper can be adjusted by speeding up or slowing down your federate. It can also be controlled using a tilting or a dynamic head control system. The image below shows some possible taper issues you can face if you do not have the correct pressure or feed-rate.
Cost
Interestingly the cost works out to be similar between routing and waterjet cutting. On one hand you have bits to continually replace and dust extraction to worry about with routing vs abrasive material and consumable likes fixtures, nozzles and orifices on a waterjet. If you are considering the purchase of a router table or waterjet, the waterjet will be more expensive. Used ones can go for $25,000-$60,000 on the low end, up to $200,000+ for a new one. New desktop waterjets have recently been introduced for under $5,000. https://www.wazer.com/. Routers on the other hand have been in the maker community for far longer and can start as low $1500 for a desktop model. For a more rigid and industrial machine capable of cutting in multiple axes, machining centers start around $40,000 and can go well over $100,000 for a 5-axis machine.
Sources:
Waterjet Basics: https://www.flowwaterjet.com/Learn/How-Waterjet-Works.aspx#basics
Rhino Board: http://www.rhinoboardwj.com/
Omax tapered edges: https://www.omax.com/news/blog/controlling-taper
Thanks Elevated Material provide me very informative information
Very good post! We will be linking to this great article on our
site. Keep up the good writing.
Thanks! Glad you like it!
Hey your points on Delamination were bang on! Very interesting to know. Thanks for the explanation.
The Komodo dragon of teeth cutting technology. I applaud the ingenuity to this overwhelmingly comprehensive technique.
Food for thought!