A Look into CNC Machining Carbon Fiber Billet at Elevated Materials
Understanding Amorphous Carbon Fiber Billets
Amorphous carbon fiber billets are at the forefront of material technology, offering a blend of strength, lightweight, and durability that traditional materials can scarcely match. Unlike laminate counterparts, amorphous carbon fibers do not have a regular layered structure, which contributes to their more uniform mechanical properties. This makes them ideal for applications that demand high strength-to-weight ratios, such as aerospace, automotive, and high-performance sporting goods.
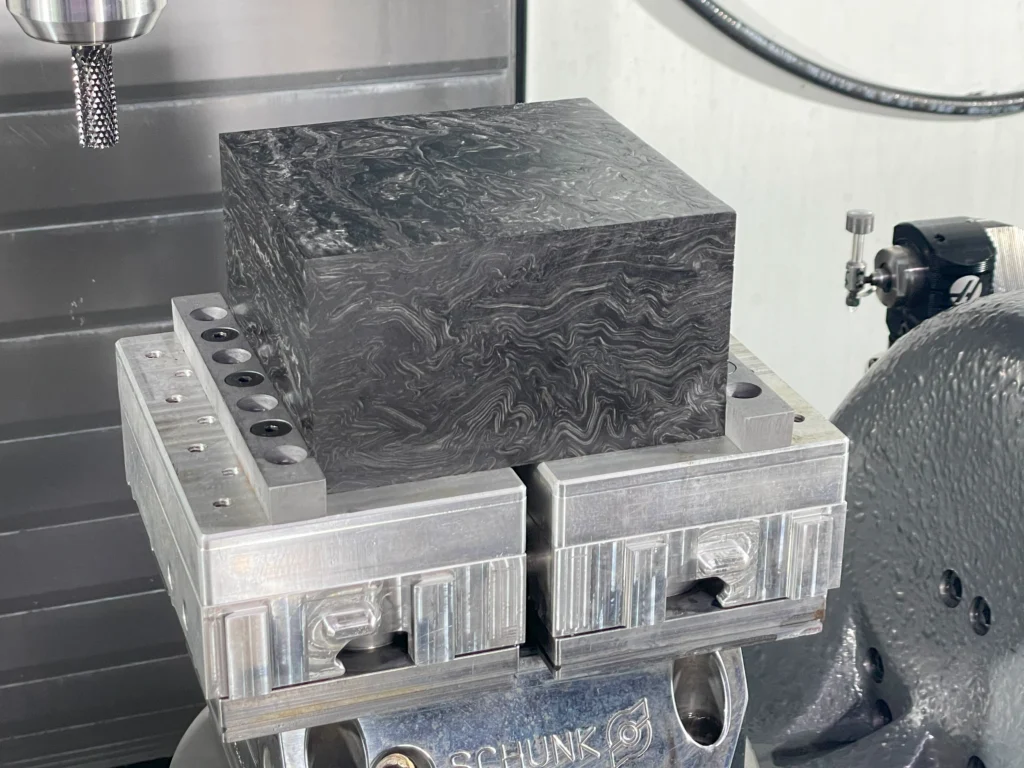
A Machining Overview
Machining carbon fiber presents unique challenges. The material’s abrasive nature can lead to rapid tool wear, while its tendency to fray or delaminate requires specialized machining strategies to maintain the integrity of the part. Additionally, the dust generated during the machining process can pose health risks and equipment damage if not properly managed.
5 Axis Cutting
The versatility of 5-axis machining carbon fiber billets unlocks new possibilities for the design and manufacturing of carbon fiber parts. Tooling techniques allow precise dimensions to be hit repeatably. Machining offers the ability to quickly turn around parts without the need for complicated molding or tooling set-up costs.
Robotic Loading and Unloading Parts
Increased Productivity: Automation allows for continuous operation, even outside of regular working hours, boosting overall production capacity. Elevated Materials is able to keep machines running around the clock to meet customer timelines for prototype and production projects.
Tooling Selection
Machining carbon fiber presents unique challenges. The material’s abrasive nature can lead to rapid tool wear, while its tendency to fray or delaminate requires specialized machining strategies to maintain the integrity of the part.
Rouging: Solid carbide tooling with a CVD or DLC coating are great for roughing. Burr-style geometries cut through material rapidly.
Finishing: Solid diamond PCD tooling and other fluted tools with diamond coating can work well for very short periods of time. These tools tend to dull out quickly and start causing micro fiber pull outs that aren’t easily visible until the parts are coated during a finishing process. Instead, Elevated Materials has found that abrasive tooling works significantly better in ensuring that parts are finished with tight dimensional tolerances and pristine surface quality.
Coolant Selection
Elevated Materials uses fully synthetic coolant to machine carbon fiber parts. Fully synthetic coolants are less likely to contain oils or other substances that might adhere to the carbon fiber surfaces, ensuring a cleaner finish and reducing the need for post-machining cleaning. Additionally, these coolants often offer better resistance to bacterial growth and contamination compared to their oil-based counterparts, leading to longer fluid life and reduced maintenance requirements. Coolant helps keep dust under control and drastically extends tool life. Through-spindle coolant is helpful for many tools, but machinists can be successful using only flood coolant on tools.
Dust Filtration
Additionally, the dust generated during the machining process can pose health risks and equipment damage if not properly managed. Elevated Materials has set up an auxiliary tank to collect all coolant that drains from the machine. Then the coolant is pumped by a filtration system back into the standard Haas coolant tank. This collected 100% of the dust generated by the machining.
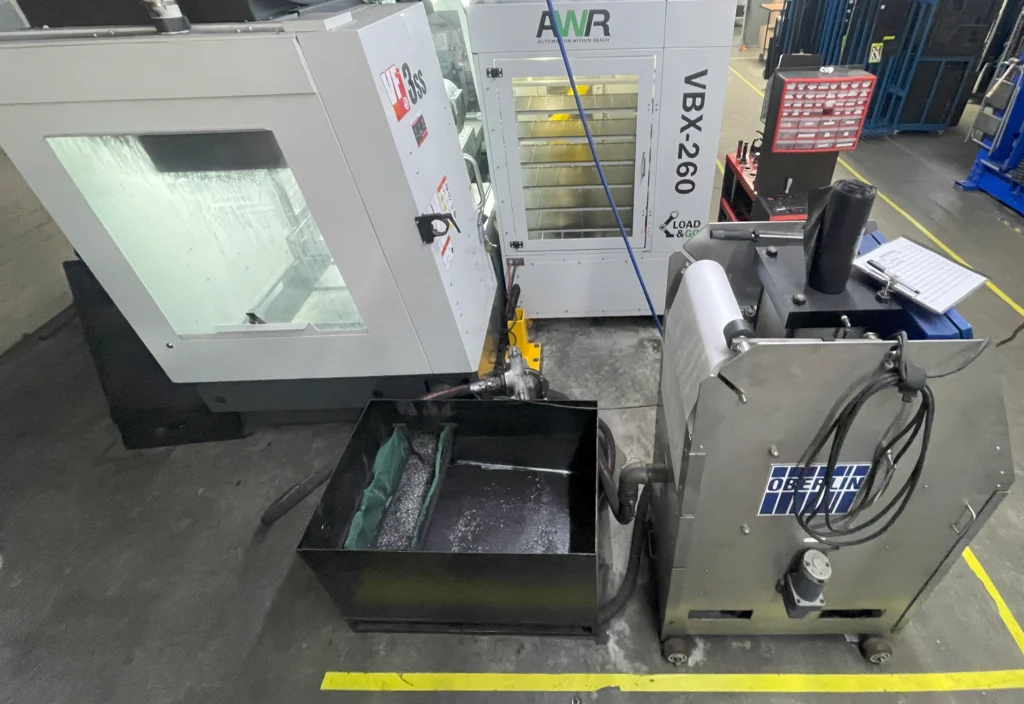
Set up a meeting with us to learn more about machining carbon fiber billets